Aarti Soerensen discusses the need for effective battery lifecycle management in the face of rapid adoption of BEVs in mining
by aartimona
The recent surge in global electric vehicle (EV) sales is remarkable.
With year-on-year growth of 35%, nearly 14 million new electric passenger cars hit the roads in 2023. By the end of 2024, that number could reach 17 million, or one in five cars, according to the International Energy Agency (IEA).
Electric cars now account for 95% of the growth in EV battery demand, which reached 750 GWh in 2023 – a 40% increase compared to the previous year. In this rapidly expanding market, US$500 billion in investments were announced in 2023 to boost battery manufacturing capacity.
By 2035, every other car sold could be electric.
While perhaps not at this pace, the shift to battery-electric vehicles (BEVs) is also gaining traction in the mining sector. A 2024 Global Data report states that in ten analysed countries, there were 11,646 BEVs operating in the sector as of 2023, including excavators, trucks, loaders and other vehicles.
The report anticipates the off-highway EV market will grow about 17.4% annually between 2023 and 2030.
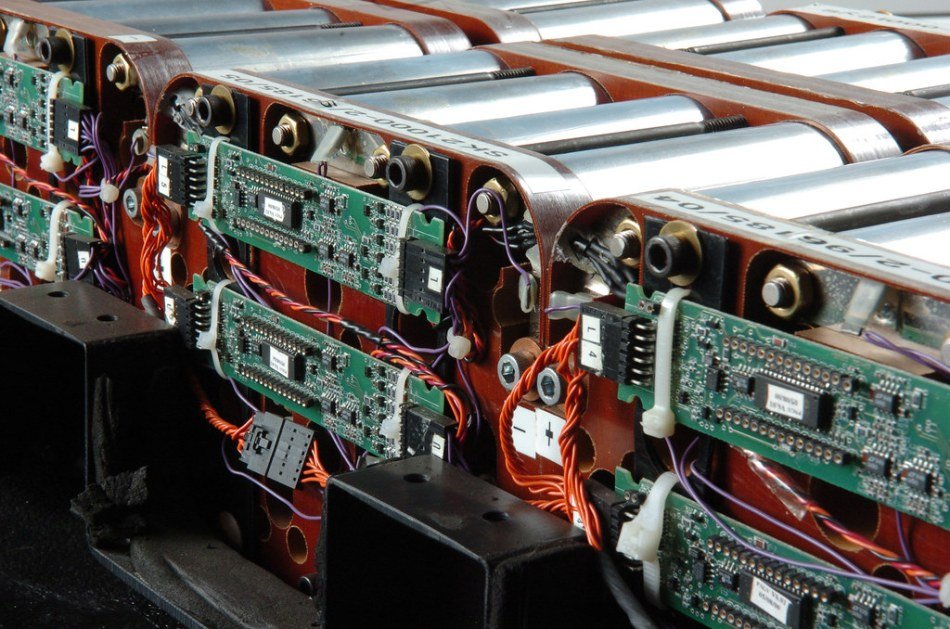
Batteries and BEVs are clearly poised to play a crucial role in the clean energy transition and in fulfilling COP28 commitments. However, while the supply and demand of materials needed to meet the growth rate of batteries and EVs have been the focus of many, sometimes controversial, discussions, a much less debated fact is this: batteries do not last forever.
The current generation of lithium-ion batteries used in mining equipment is expected to last at least 3,000 full charge and discharge cycles before their capacity drops to 70%–80% of their initial value.
When battery life degrades to 70% or even 60%, depending upon application requirements, it needs to be replaced. For a heavily used mining truck, this could be as soon as after three years. A loader battery might last four years or longer due to lower average power demands and fewer daily swaps.
A lifespan of three to four years is not a long time, and it’s certainly not too soon to start thinking about what to do with all these decommissioned batteries, as they could present a serious waste-management challenge for miners that’s rapidly (and quietly) approaching.
Three main options exist for managing battery waste: reducing material wear, reusing or repurposing batteries for a second life, and recycling. Let’s examine each option and how they’re being applied in the mining sector.
Reduce: extending battery life
One way to reduce battery wear and extend the lifespan is by optimising battery usage across the mine fleet. For example, where applications are interchangeable, newer batteries could be assigned to higher-power tasks, like trucks driving up ramps, while older batteries could be repurposed for lower-power applications, such as loaders.
This approach maximises battery utilisation and prolongs the time before replacement is needed. Sandvik’s interchangeable battery modules, for example, make this strategy feasible.
Another approach, though beyond miner’s direct control, involves using higher-capacity battery technologies to extend their expected life. For instance, Sandvik’s latest battery pack offers 36% more energy in the same footprint, enabling trucks and loaders to operate longer between swaps, with improved cooling to reduce cell degradation.
As battery technology evolves, we can expect further improvements in energy density, lifespan and recyclability. Although miners may not have direct control over these advancements, their feedback to OEMs will be crucial in research and development efforts, and in reducing waste from decommissioned batteries.
Reuse: finding new purposes for old batteries
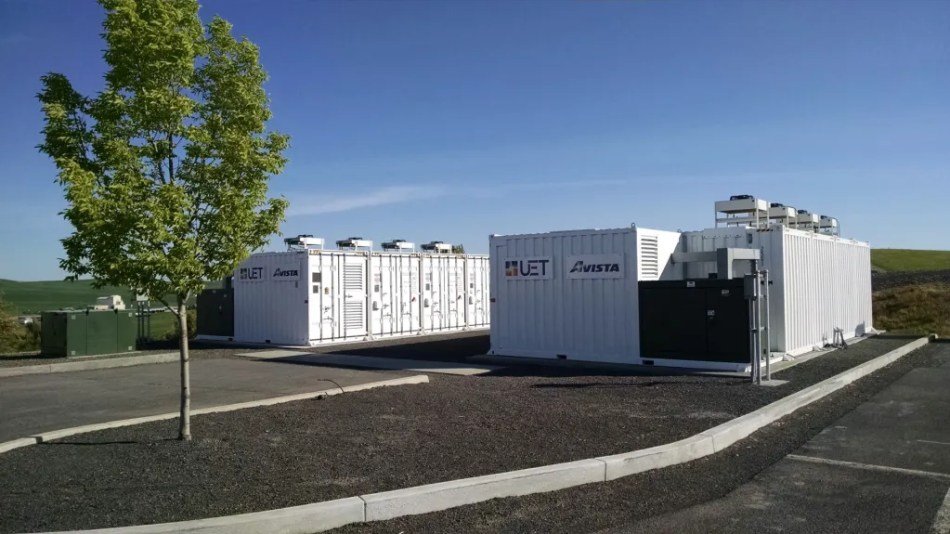
As EV battery performance declines, they can be repurposed into stationary power storage units; a growing component of electrification and emission reduction efforts in the mining sector.
The economic feasibility of battery reuse depends on factors like the end-of-life battery’s selling price, remaining lifespan, and electricity market rates, but it presents a promising option for mining companies.
Even though ‘batteries as a service’ (BaaS) has emerged as an alternative business model – one that ensures extended producer responsibility – according to a recent article in IM, Epiroc recently stated that “more and more customers want to have the full ownership of the complete equipment, including battery”.
This means that miners typically own the batteries with their equipment, and that the responsibility for end-of-life management lies with them. In this case, repurposing batteries on-site could improve circularity and reduce carbon footprints.
Sandvik and Glencore are pioneering this approach with a pilot project to repurpose 128 Sandvik battery modules into a 1MWh battery energy storage system (BESS) at a Glencore mine.
The BESS will be housed in a 20-foot container equipped with additional Sandvik systems for battery management and monitoring, energy management, as well as fire detection and prevention.
To start, the BESS will power mine services, such as lighting and light EV charging, while Sandvik and German ECO STOR, a second-life energy storage system provider, are exploring the feasibility of using the second-life batteries for power shifting, peak shaving and arbitrage.
The prototype BESS container should be operational by 2025 and a fully commercialised option available by 2026.
Epiroc and Renewmic also recently announced a collaboration to create a battery storage solution utilising second life batteries from Epiroc. Previously used to power electric mining equipment, the batteries are now being used to support and stabilise the Swedish power grid through frequency containment reserve (FCR) services.
While ownership and business models for second-life batteries are yet to be finalised, if BESS becomes a commercial offering, collaboration between mining companies and OEMs could significantly extend battery life, yielding substantial environmental and economic benefits.
If successful, the useful life of BEV batteries could be as much as doubled, bearing enormous environmental and, hopefully, equally attractive economic benefits.
Recycle: waste not, want not
Once batteries hit the end of their (hopefully) second life, they must be decommissioned and, in the best case, get fed back into production through material recycling.
Unfortunately, recycling rates for EV lithium-ion batteries are nowhere near where we need them to be: the current rate is estimated at less than 5% due to the cost and complexities of battery recycling methods available to date. If batteries end up in landfill, they present a considerable hazard to both water and soil.
The battery recycling space is a dynamic one, with players like the American Battery Technology Company (ABTC), Redwood Materials – which is headed by Tesla co-founder JB Straubel – and Canada-based Li-Cycle emerging with ambitions to move the needle on recycling technology development, and commercial-scale recycling facilities across the globe.
Figures show that this is sorely needed; Li-Cycle estimates that by 2030, a total of 15 million tonnes of lithium-ion batteries will reach their end of life and will need to be recycled.
Since the nature of the methods used in virgin metal extraction and in the recovery of metals from e-waste or batteries are not dissimilar, there certainly is room for miners and refiners in the emerging battery recycling market, which McKinsey estimates to increase three-fold by 2040, with revenues expected to exceed $40 billion.
Indeed, strategic partnerships and joint ventures are emerging in this dynamic landscape…
In January 2024, Anglo American announced a strategic partnership with GEM, one of China’s largest battery and battery material recyclers, to explore new metal dissolving technologies that allow for more efficient use of battery materials, from mined as well as recycled routes.
In March this year, Li-Cycle announced a $75 million strategic investment from Glencore to build upon their existing partnership as part of Glencore’s ambition to bring more circularity to the battery materials space.
This investment follows a joint study that was commenced in 2023 for building Europe’s largest battery recycling plant on the Italian island of Sardinia by 2027.
Belgian, once miner and now refiner and recycler, Umicore, has developed a cutting-edge recycling system that melts down the core components into a metal alloy (including copper, nickel, and cobalt) and a concentrate (containing lithium and other rare elements).
This utilises the batteries’ own energy and organic materials so that only little energy needs to be added to reach the temperatures required for smelting.
Umicore’s site in the Hoboken district of Antwerp already has the capacity to recycle the equivalent of 35,000 EV batteries a year, which makes it one of the largest in the world.
Working towards circular value chains
With such dynamic growth in the EV market, including in mining, one fact is undeniable: batteries and EVs are part of the solution, but they are by no means a silver bullet to decarbonising transport.
On the contrary, they clearly come with their own set of challenges and unresolved questions, especially with respect to battery recycling.
The urgent need for technological innovation to efficiently recover valuable materials from decommissioned batteries cannot be overstated. Developing low-impact recycling methods is essential to reducing the overall carbon footprint of batteries and addressing potential shortages in virgin material supplies.
However, significant unresolved questions remain. For example, who will take responsibility for collecting spent batteries, especially from remote mine sites?
Companies like Redwood Materials are pioneering solutions, such as an online platform to register and collect used EV battery packs, but it remains unclear how these initiatives will extend, for example, to challenging locations like the Arctic Circle or African deserts.
An even bigger challenge lies in whether battery manufacturers, mining companies, and OEMs can collaborate to create a closed-loop circular supply chain that includes the collection, recycling, reuse, or repair of used Li-ion batteries.
While recent efforts by Glencore and Anglo American are promising, the issue of more widespread effective collection still needs to be addressed.
To conclude, the benefits of establishing a circular value chain for EV batteries are substantial, but there is still a long way to go. As the volume of decommissioned batteries continues to grow, strategic partnerships between mining companies, battery manufacturers, and recyclers will be essential in addressing all three options of reducing, reusing, and recycling.
Ideally, the future approach of life-cycle management for mining EV batteries will encompass all three options to close the loop on battery materials and mitigate the looming e-waste challenge.
Published by The Intelligent Miner
The post Mining’s electric challenge: managing end-of-life EV batteries appeared first on American Battery Technology Company.