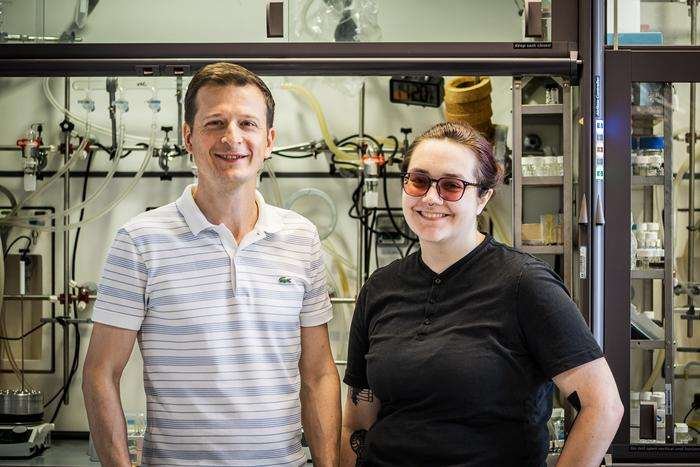
A Czech group has developed a new method of separating the rare earth elements, or lanthanides, which are widely used in the electronic, medical, automotive, and defense industries. The seemingly unique method allows metals such as neodymium or dysprosium to be purified from used neodymium magnets. The supposedly environmentally-friendly process precipitates the rare earths from water without organic solvents or toxic substances. The results were published in the Journal of the American Chemical Society (JACS) at the end of June.
Global demand for rare earths is driven primarily by their use in extremely strong neodymium magnets, which enable efficient conversion of motion into electrical energy and vice versa. They are essential to manufacturers of electric cars, wind power plants, mobile phones, computers, and data centers. As these industries develop, demand for rare earths will continue to grow. However, the process of mining and purifying these elements is highly energy intensive and produces large amounts of toxic and radioactive waste.
The rare-earth market is dominated by China, and it is considered strategically advantageous for US and European sourcing to focus on so-called urban mining, i.e. the recycling, renewal, and reuse of materials from discarded equipment, such as electric vehicles.
“In the future, we won’t be able to cover the growing consumption of rare earths with primary mining. We know that within ten years at the latest, it will be necessary to manage these materials more carefully. In order to achieve this, the development of new technologies must start now,” said Miloslav Polášek, head of the Coordination Chemistry group. “Our method solves the fundamental problems of recycling neodymium magnets. We can separate the right elements so that new magnets can be produced. Our process is environmentally friendly, and we believe that it will work on an industrial scale. Fortunately, unlike plastics, chemical elements don’t lose their properties through repeated processing, so their recycling is sustainable and can compensate for traditional mining.”
The topic, which Polášek’s group has been working on for a long time, is part of Kelsea G. Jones’s doctoral thesis. “We’ve developed a new type of chelator, which is a molecule that binds metal ions. This chelator specifically precipitates neodymium from dissolved magnets, while dysprosium remains in solution, and the elements are easily separated from each other. The method is also adaptable for the other rare earths found in neodymium magnets,” said Jones. “The separation is done in water and generates no hazardous waste. We achieve the same or better results than current industrial methods that rely on organic solvents and toxic reagents.”
The new technology is patented and responds to a fundamental global problem at the right time. “We’re impatiently awaiting the results of a feasibility study, which will help us direct this research from the laboratory into practice. I believe that in cooperation with the investors and business partners we’re approaching, this new technology from IOCB Prague has the potential to influence a wide range of industrial sectors,“ says Milan Prášil, director of the transfer company IOCB Tech.
The research also appears to have highlighted a puzzling knowledge gap, in that Polášek’s team discovered that the element holmium is used in neodymium magnets of newer electric cars, a finding that emerged from analyzing samples from the electric motors of European and Chinese cars. According to the group, this is a detail so far omitted from any professional publications on these kinds of magnets, and so it is also omitted from recycling protocols when processing waste from electric cars. So the finding suggests the possibility of rectifying the omission.